Each year, more than 350,000 tons of wood, mostly lumber and pallets, is ground into chips (often referred to as “hog fuel”) and burned as fuel in industrial boilers in the Puget Sound region, releasing the rough equivalent of one million metric tons of CO2. If we assume, based on past research, that half of the 350,000 tons of clean wood is reusable dimensional lumber, that equates to more than 100 million board-feet per year (at 800 board-feet per ton).
For years, the lack of a simple method to capture and process this wood, as well as a place to do so, has been the biggest hurdle to creating a more circular system of wood use… until now.
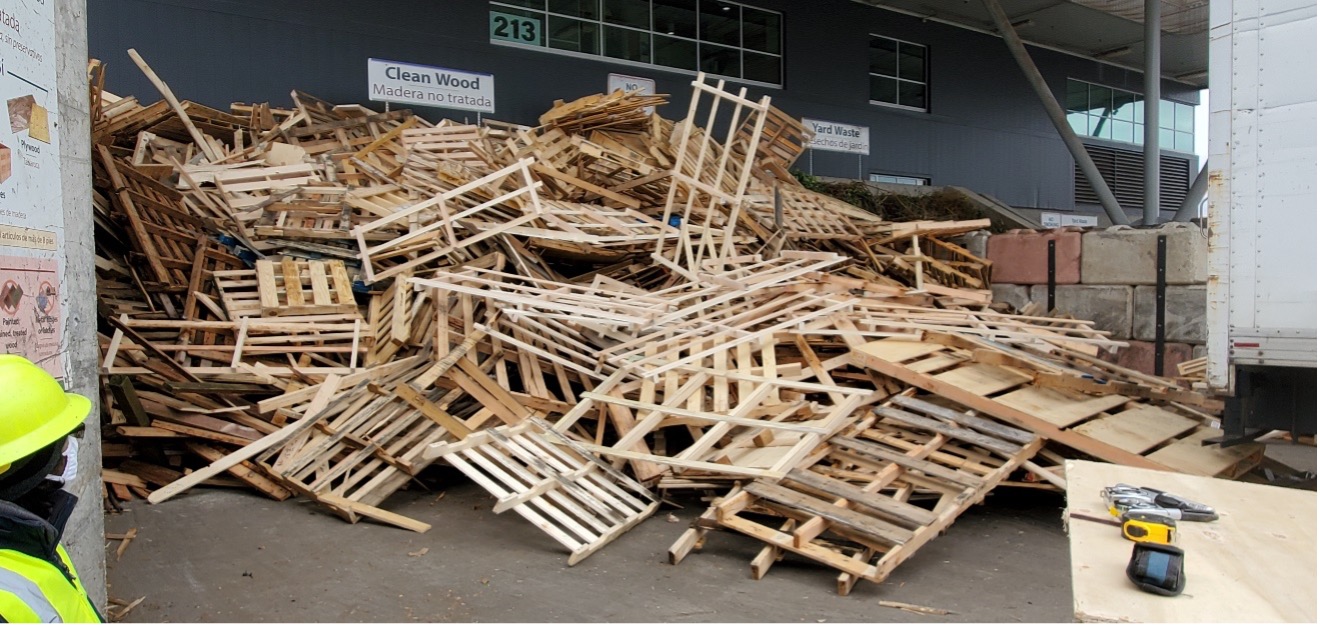
Unpainted/untreated wood collected at King County’s Bow Lake transfer station
Technology and research advances
Recently, Urban Machine created an automated, in-line machine to de-nail and process wood into useable dimensional lumber which is then finger-jointed for manufacturing into dowel laminated timber (DLT). Likewise, Urbanjacks in British Columbia is finger-jointing reclaimed dimensional lumber for use in various applications. These two companies are leading the way for what numerous university studies already show is feasible: the structural reuse of lumber in mass timber. A 2021 study from King County showed that much of the wood “waste” collected at transfer stations would, after processing, be suitable for finger-jointing and use as feedstock for mass timber such as glulam, DLT (dowel laminated timber), NLT (nail laminated timber), CLT (cross laminated timber) – or even wood fiber insulation.
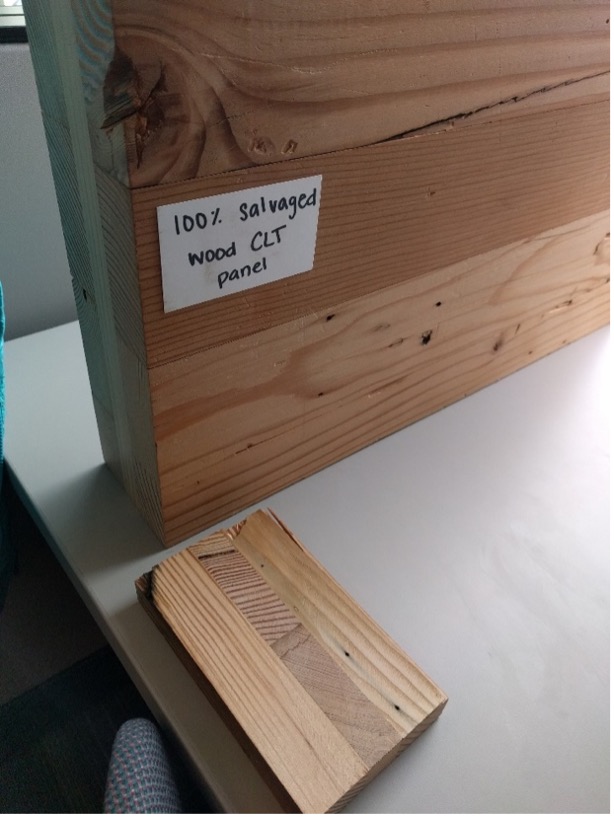
Sample test panel of cross-laminated timber (CLT) made from 100% salvaged lumber at Oregon State University
Local progress
Many Puget Sound area companies offer deconstruction and salvage services. Much of what they capture is as good as, if not better quality, than new wood, but they currently lack robust reliable markets for all the reclaimed/salvaged lumber that they are able to harvest. Recent local and state policy changes seek to support deconstruction and material reuse. Seattle and King County have bans on wood disposal. State building code allows salvaged lumber to be used without grade stamp (in both residential and commercial construction) and also encourages salvage assessments and deconstruction. King County offers local deconstruction trainings and Seattle has financial deconstruction incentives. There is a groundswell of opportunity to reuse more wood and divert it from landfill burial and burning in boilers.
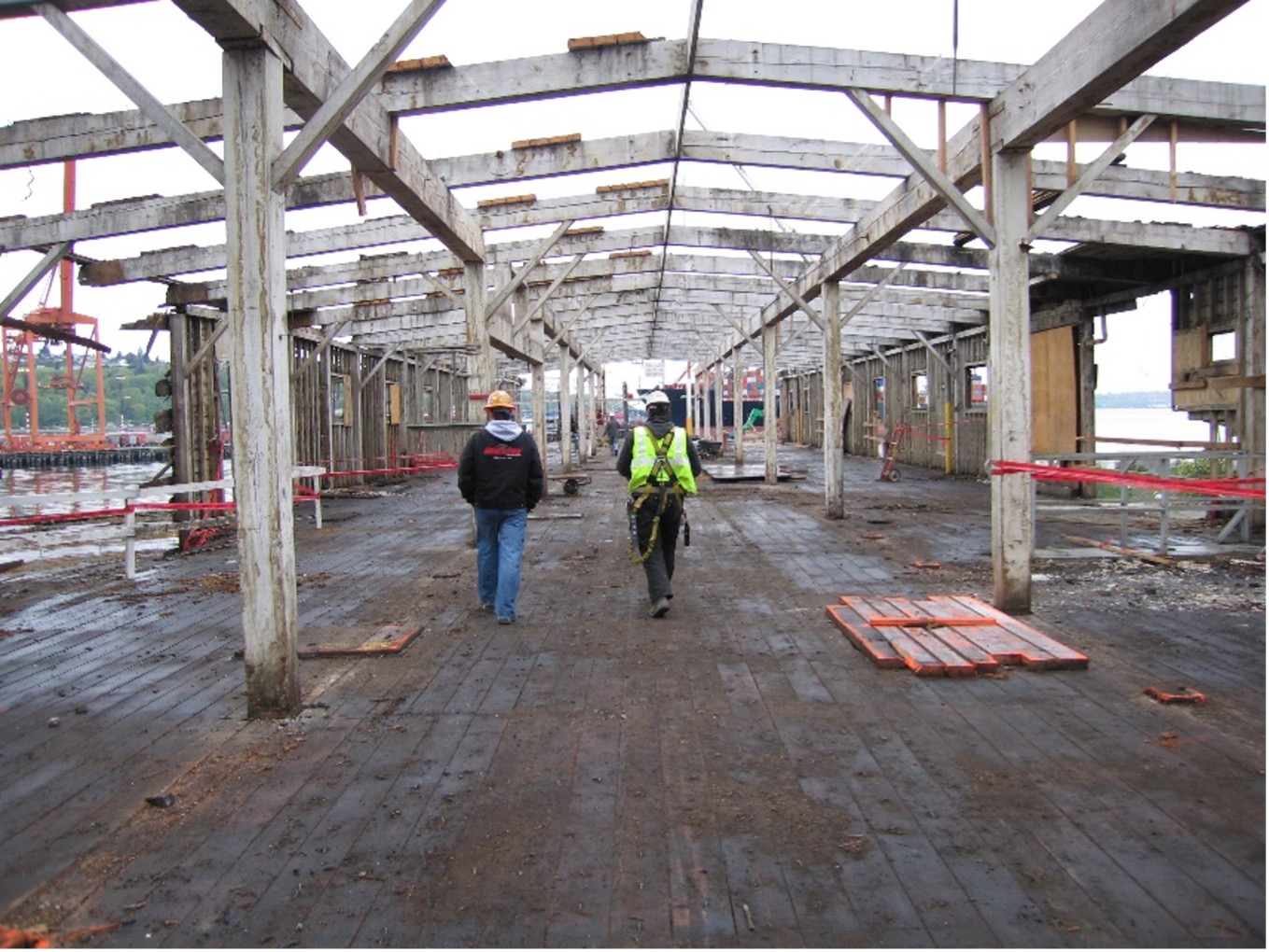
Deconstruction of King County’s Warehouse C at the former Fisher Flour Mill on Harbor Island
The City of Seattle is accepting proposals until 1pm on Feb. 11 to operate a Salvaged Lumber Warehouse to collect, process, grade, inventory, and coordinate reuse and distribution of salvaged lumber – a key missing piece in the circular economy puzzle. King County’s Executive Climate Office has been awarded federal grant funds to support this effort. The grant dedicates funding in 2025-2030 for additional collection locations and end market development in coordination with a successful Salvaged Lumber Warehouse.
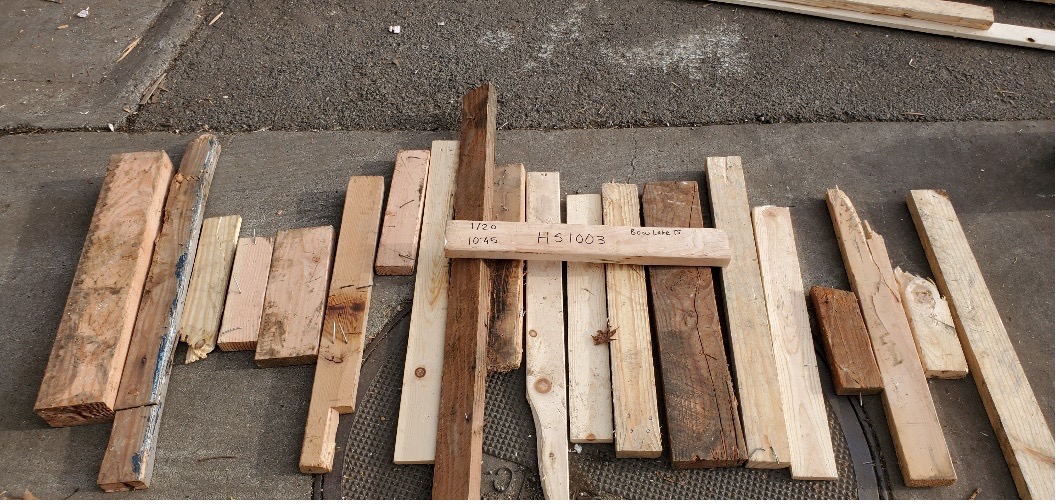
Sample of lumber collected at Bow Lake transfer station
Learning from others
San Antonio’s Material Innovation Center and the Oregon Mass Timber Coalition’s T2 Building Innovation Hub are demonstrating how partnerships can create opportunities for reuse and innovation, something King County wants to replicate and support. There are many mass timber suppliers in the Pacific Northwest, at least one of which, Vaagen Timber, has already tested salvaged lumber feedstock.
In the Netherlands, an apartment building was built with C-CLT (circular cross-laminated timber) made from reclaimed pallet wood. In London, UK CLT and Univ. College London built a prototype glulam and CLT structure from 100% reclaimed (“waste”) timber. Woodcircles is an EU project to develop circular solutions for wood in construction such as an “urban sawmill.” And beginning in 2025, dozens of universities, businesses, and organizations across the U.S. will quantify the embodied carbon benefits of construction materials made from reused wood with new lifecycle assessments (LCAs) and environmental product declarations (EPDs).
In 2021, Seattle and King County funded demonstration projects with local businesses to collect, process, and reuse more wood. Since then, King County Re+ Circular Economy grants awarded to Earthwise Architectural Salvage, Re-Use Consulting, and Second Use supported expanding reuse and collection opportunities.
Taking action
King County will continue to offer deconstruction and environmental literacy trainings in collaboration with local community-based organizations. Local jurisdictions are encouraged to support the diversion and reuse of lumber (and other building materials) by adopting WA state building code appendices P, Y, and Z which contain salvage assessment and deconstruction requirements.
Builders and architects can consider not only the benefits and incentives of deconstruction but also framing packages with FSC certified recycled/reclaimed lumber and forthcoming EPDs for salvaged materials.
Corporations and property investors can make under-used warehouse or yard space available to salvaged lumber processors – possibly qualifying for tax credits while having a watchful presence on your property.
Contractors interested in tapping a labor pool that has been trained in salvage and deconstruction should reach out to King County regarding employment of the graduates from our training program. For the last two years, King County has organized two cohorts of Green Workforce Development Trainings to build capacity in the industry with deconstruction and salvage expertise.
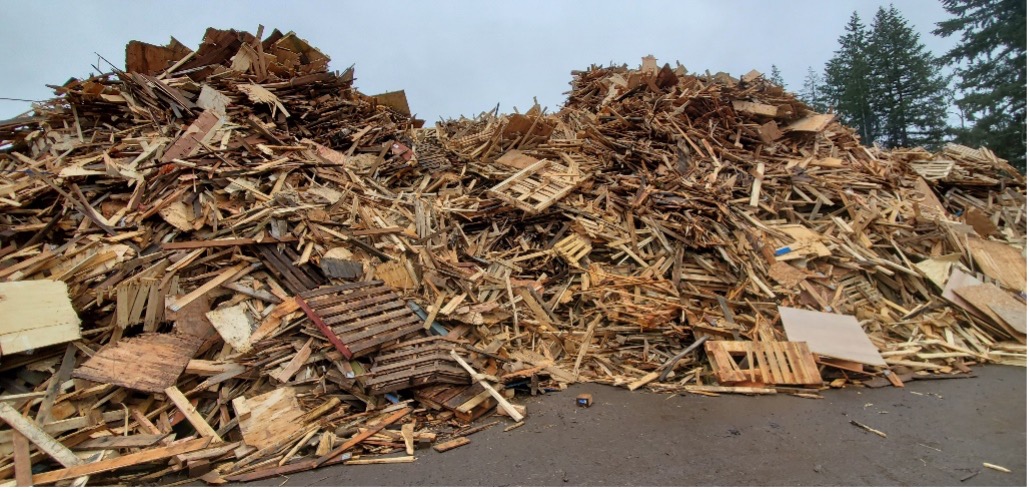
Clean wood waiting to be turned into either fuel or mulch by a local processor
In summary
Lumber salvaged from homes and commercial properties has strong potential to fill the anticipated construction lumber gap expected in Washington State’s transition to sustainably managed forests.
Between the growing interest in mass timber and the pool of local manufacturing and technology, there is an enormous supply of salvaged lumber, with low embodied carbon, that has yet to be tapped for its highest and best use: as feedstock for mass timber, engineered wood products, and other applications.
About the Author
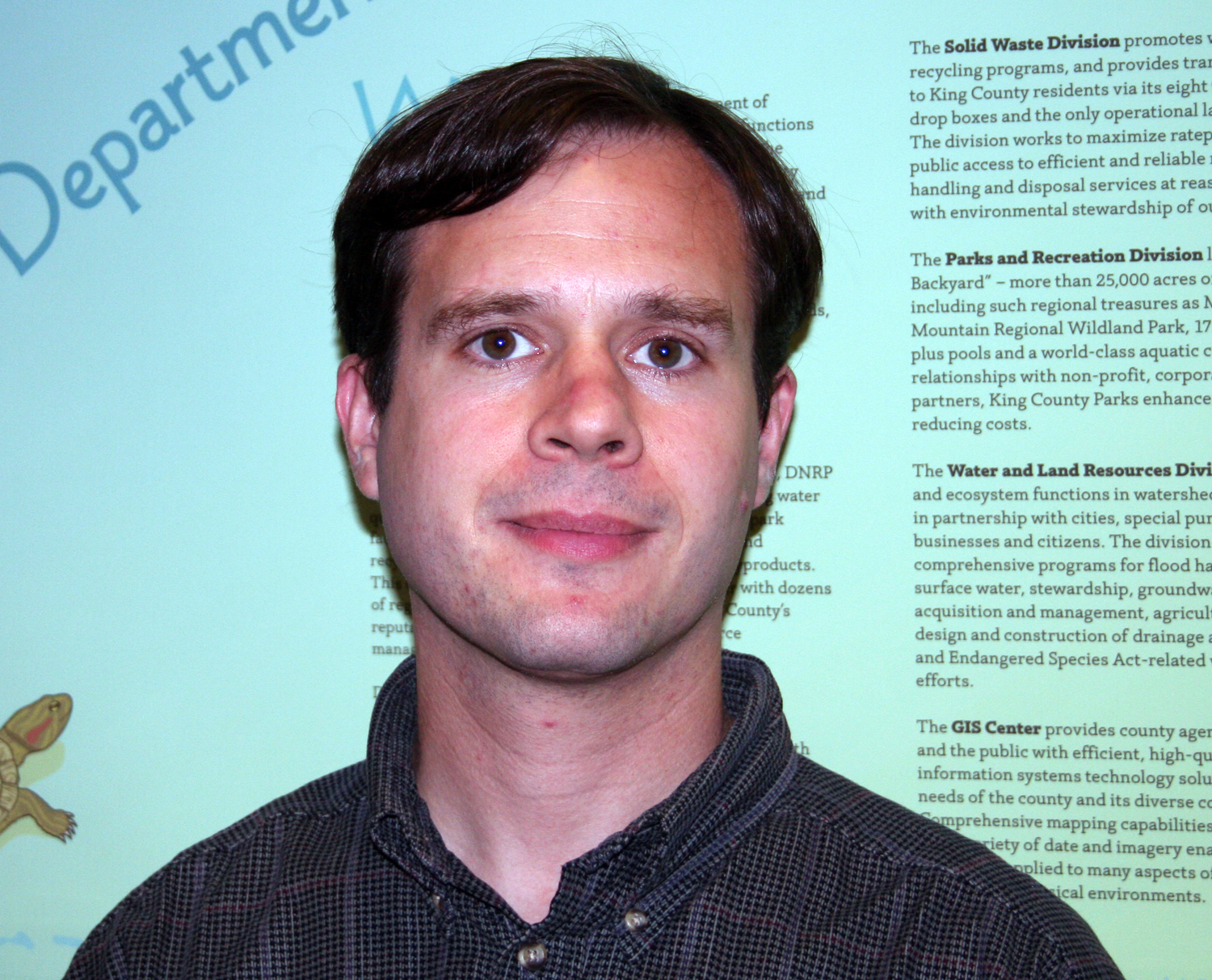
Kinley Deller manages the King County Construction and Demolition (C&D) materials diversion program and serves as a catalyst for the development of circular economies for salvaged lumber and other C&D materials. Building on over 29 years experience in the waste reduction field, Kinley is well versed in deconstruction and building salvage practices. He has been instrumental in promoting the local reuse of salvaged wood and the concept of design for disassembly to maximize the potential for future building reuse.